Continuous Improvement in Rail Engineering
Examples of Continuous Improvement
in Rail Engineering
Continuous improvement is an approach where all staff seek out, support and implement changes to make the services and products they provide better quality and more cost-effective.
The benefits of continuous improvement are substantial and more valuable at a time when financial budgets are severely constrained. Through making better use of our own and others’ expertise, everyone can make a difference to their organisation’s quality, cost-effectiveness and impact. However, continuous improvement cannot easily be achieved if you are constantly firefighting or being reactive to the everyday whirlwind.
How much time is wasted by Rail Engineers and Technicians hunting for tools, drawings, schedules and instructions daily? It’s considerable – which comes at a high cost to the business. This is the starting point for applying continuous improvements.
So, what can be done?
The application of Workplace Organisation (5S) is arguably the main starting point of any Lean Six Sigma journey. 5S is defined as a key methodology that results in a clean, uncluttered, safe, and well organised workplace. This helps reduce waste and optimise productivity. It is not just a one-off tidy up activity. 5S is all about creating an environment which facilitates sustainable orderliness and cleanliness through creating a visual location for every required item in a work area (anything that casts a shadow). Abnormalities become immediately apparent to the eye. This helps to create that ‘visual factory’; everything that is needed is at hand for immediate and ease of use. It is designed to help build a quality work environment, both physically and mentally. The 5S condition of a work area is critical to employees and is the basis of customers’ first impressions.
Now that the application of 5S is active, consider the application of Total Preventative Maintenance (TPM). Total Preventative Maintenance is a set of techniques which ensures that each machine or equipment used in a process is always able to perform its required task. This is done by placing the emphasis on staff being trained to handle routine maintenance on a regular basis – they feel empowered, with a shared responsibility for the equipment. The TPM technique will help to improve efficiency, reliability and quality, will extend the life of machines and equipment, empower staff and teach new skills demonstrating respect for people and allows highly trained maintenance staff to focus on value-adding activities.
Continuous Improvement in Rail Engineering
Rail engineering is no different to any other engineering discipline in that problems will always be encountered. Therefore, the next lean transformation and continuous improvement is the problem-solving technique.
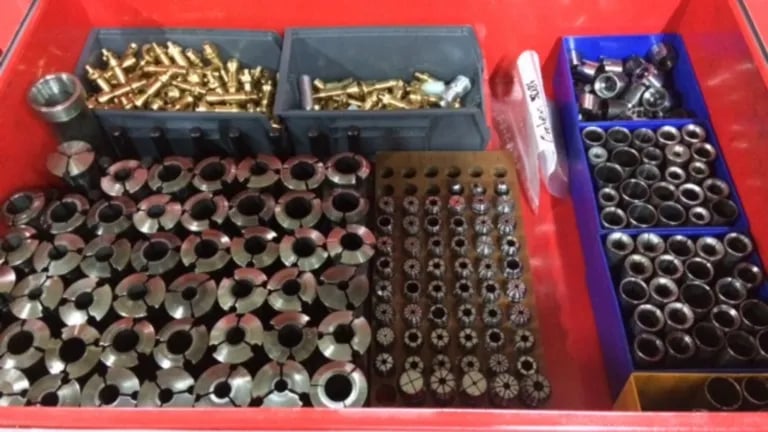
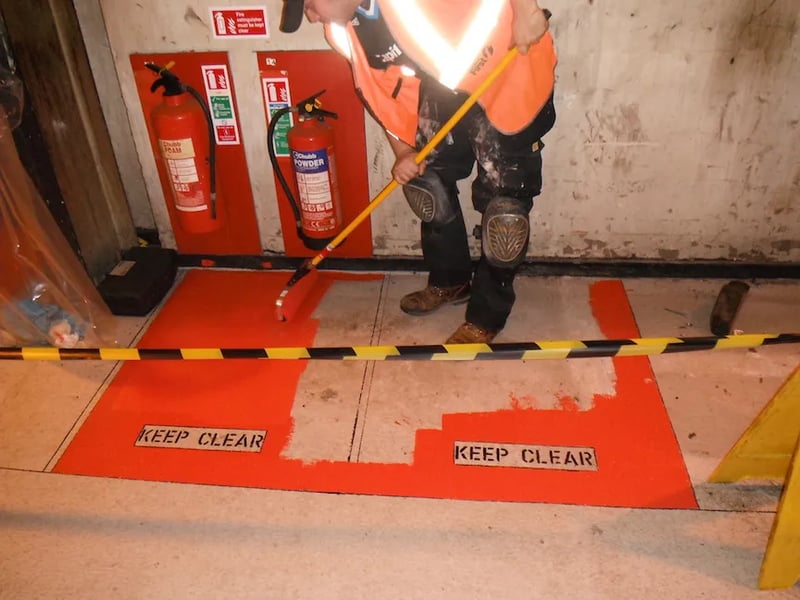
Solving problems in a Rail Engineering setting is an important part of the lean methodology. Using lean strategies, a company can better identify what problems exist, pinpoint the root causes and come up with the right solutions to get the best results. Learning about how to effectively use problem-solving techniques can help any business to improve and become more efficient. When working to make improvements in any business setting, it is important to start by identifying problems or potential problems.
Solving existing issues is a great way to eliminate waste and improve efficiency quickly. For many businesses, this is the ideal way to create a competitive edge that will help success. This is where root cause analysis (RCA) is an important factor and techniques such as the 5 Whys or Cause and Effects Analysis become effective. Root cause analysis is a structured problem-solving method. The aim of RCA is to identify, understand and solve the deeper ‘root causes’ of problems. RCA is built on the principle that causal relationships exist for all events. By understanding these, businesses can move beyond the symptoms and address the root causes at source. High quality cause and effect analysis adds a deeper understanding, leading to targeted and more effective solutions. If these are clearly documented and shared, everyone can learn from past failures and prevent future problems.
Processes
Another key area to focus on are the processes. If you concentrate on nurturing the process, the results will come as a natural consequence. Rail Engineering organisations have processes and every process within this field has scope to be improved. Unintended variation in these processes leads to undesirable variation in the outcomes of these processes. A proper continuous improvement focus is to simplify the process, proactively eliminate the opportunities for errors and you get continuous improvement and identified value. Once the value (end goal) has been determined, the next step is mapping the “value stream,” or all the steps and processes involved. The goal is to identify every step that does not create value and then find ways to eliminate those wasteful steps. Then consider the future state and how processes can be streamlined with Lean Six Sigma projects.
Also, conduct Gemba walks to identify any of the eight wastes in these processes and apply Kaizen methodology of small constant improvements to reduce and eliminate the wastes identified.
Regular continuous improvement will develop a new organisational culture which will embed this philosophy into everyday practices. Lean Six Sigma will help management to develop empowered employees to identify and drive improvement ideas on a far more regular basis which is a sure-fire way of keeping ahead of your competitors.
Share this
You May Also Like
These Related Stories
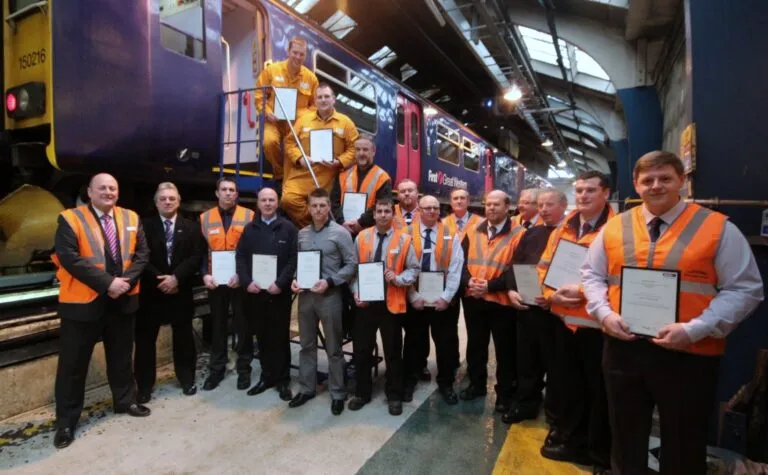
Training for the Rail Industry
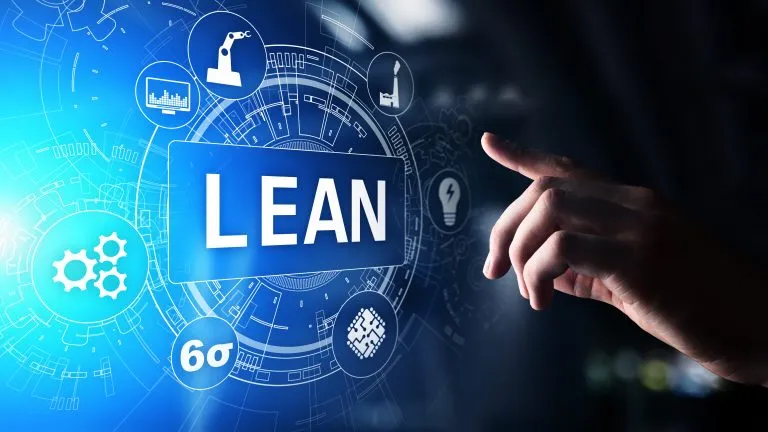
Lean Manufacturing operative EPA
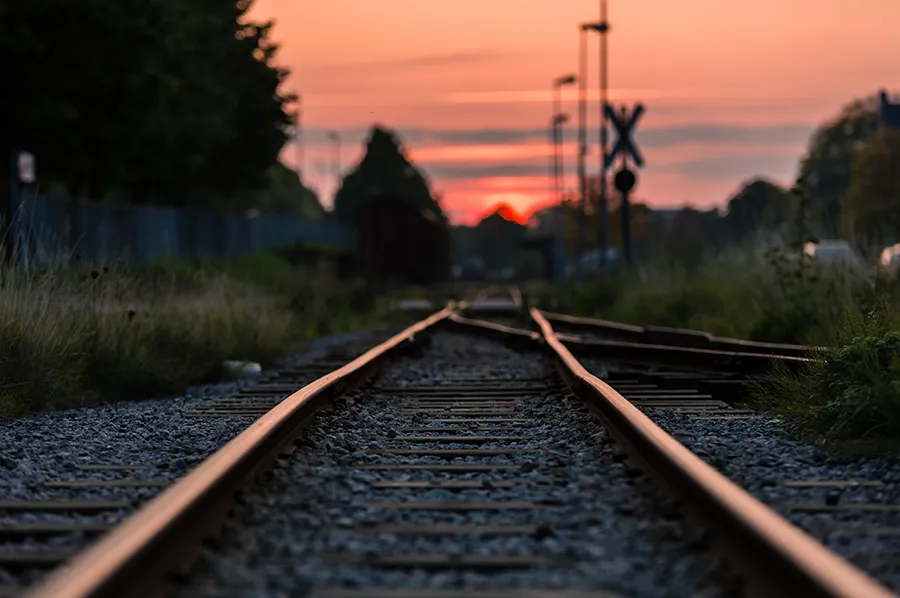
No Comments Yet
Let us know what you think