Top skills your Rail Engineers need for process waste management
Lean thinking aims to remove wastes from work processes. Before diving into the 8 wastes, it is important to understand what waste really is. Waste is any action or step in a process that adds no value to the customer. In other words, waste is any process that the customer does not pay for. This is classed as non-value-added waste and becomes an unnecessary cost to the business.
Wastes
The original seven wastes (Muda) was developed by Taiichi Ohno, the Chief Engineer at Toyota, as part of the Toyota Production System (TPS). The seven wastes are Transportation, Inventory, Motion, Waiting, Overproduction, Over processing and Defects. They are often referred to by the acronym ‘TIMWOOD’. The 8th waste of non-utilised talent or ‘Skills’ of workers was later introduced in the 1990s when the Toyota Production System was adopted in the Western world. As a result, the 8 wastes are commonly referred to as ‘TIMWOODS’.
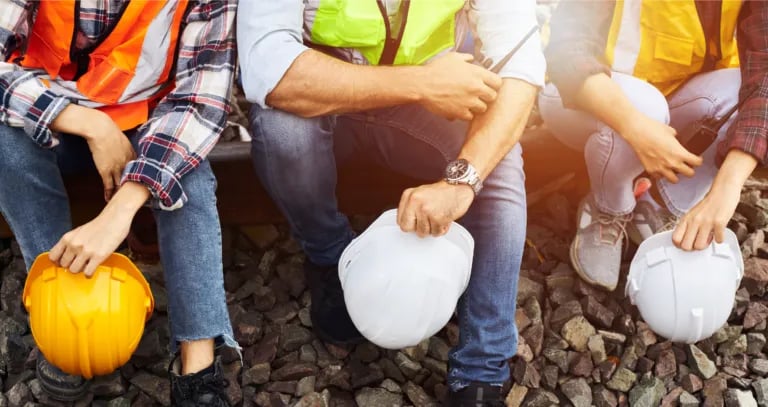
Wastes in Railway
Now, where to start and what wastes are present in a rail engineering environment?
Motion waste springs immediately to mind with so many engineers and technicians travelling for information, walking to deliver paperwork, looking for that right tool that is needed for the job, collecting spare parts from stores or quite simply, hunting down a decision. Arguably, another is transportation waste with the movement of parts, resources and information key issues due to poor layout.
Motion and Transportation wastes both occur when people, equipment, products and information, move around without creating value. These consume unnecessary resources such as time and manpower, when clear focus on completing maintenance schedules and repairs add value that the customer is paying for. Simply do the maths; how much is this costing the business? It must be substantial and really need solutions to either eliminate or reduce it, just to stop the haemorrhaging of cash. It is always good to measure the waste, to clearly see the price you are paying. and determine the priority and difficulty of eliminating it.
Value Stream Mapping
The first step to reducing wastes is to recognise that they exists. It’s important to have an effective process in place to identify them. Therefore, Rail Engineers and Technicians need to learn, practice and implement the top skill of Value Stream Mapping (VSM). This is a lean management method and powerful technique for analysing the current state and designing a future state of a given process. It shows the flow of information and resources such as materials and manpower as they occur and is an effective tool for mapping out the process involved. It does this by displaying the relationship between production processes in a visual format, separating value-added and non-value-added activities.
Use the Value Stream Mapping technique to identify wastes and start with the end customer in mind. Remember: the end customer can be internal as well as external to the business.
Then, work backwards from the end customer identified all the way to the start of the production processes. Factor in key elements such as cycle times, any changeover times, available capacity, and value-added time. Then, document instances of the 8 wastes in the process and develop a plan for eliminating or reducing these.
Remember, Value Stream Mapping is a team exercise focusing on collaboration which takes a thoughtful approach and requires buy-in at all levels. The art is to continue challenging the process team to identify more wastes and to continuously improve your key processes. This in turn will maintain your competitive advantage.
Do not stand still, continuously engage with all members of the engineering team and elicit their ideas for improvements.
As the team identifies more wastes and improves efficiencies, they will become more confident in their own problem-solving capabilities. Then, over time, reducing wastes will become a key initiative and part of everyone’s daily routine
The main benefits of Value Stream Mapping in rail engineering are that it helps to determine the actual sources of wastes and contributes towards reducing or eliminating them. Then, once hand-off points are made visual, the engineering team can focus on stopping them from re-occurring through enhanced communication and behaviours. Finally, it helps to prioritise end results which are of customer value and directs focus towards these identified values.
Gemba
Another key practice for Rail Engineers applying lean thinking, is to learn and regularly participate in ‘Gemba or Waste Walks’. When it comes to Continuous Improvement, the best improvement ideas will come from going to Gemba (Place of work) and walking the process for yourself. If your objective is to identify waste, there is no substitute for ‘going to the work’ and there are things that can only be learned by watching the work with a purpose. Thus, a Gemba walk, or waste walk, is an activity that takes members of the rail engineering team, including management, to the front lines. Here, they can look for waste and opportunities for improvement, observe the work where the work is being done and identify what goes wrong or could go wrong, how often it does or could go wrong, and the associated consequences. It is designed to help everyone understand the value stream and its problems.
In summary, no business is immune to waste processes. Eliminating these waste processes sounds easy, but reality tells us it takes time and effort. When you see the benefits of eliminating waste you get the motivation to do it more and more. Eliminating waste is also part of the Kaizen philosophy in lean production. Kaizen is a competitive strategy in which all employees work together to create a strong culture of constant improvement, and part of becoming better and better is improving efficiency and eliminating all waste. A key point to remember as quoted by Shigeo Shingo:
“The most dangerous kind of waste is the waste we do not recognise”.
Finally, remember that identifying these process wastes will help you optimise resources and increase profitability. It will also help you realise the exact elements of work processes that can be improved upon and it will enable you to see if a work-based activity is necessary or is just simply, pure waste.
Share this
You May Also Like
These Related Stories
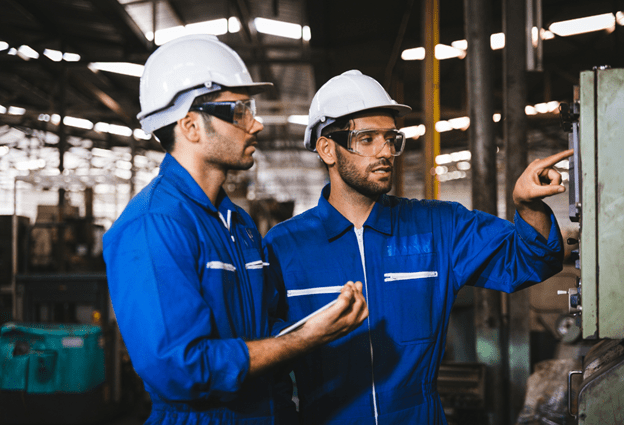
How A Pre-Employment Course Can Help Launch Your Engineering Career
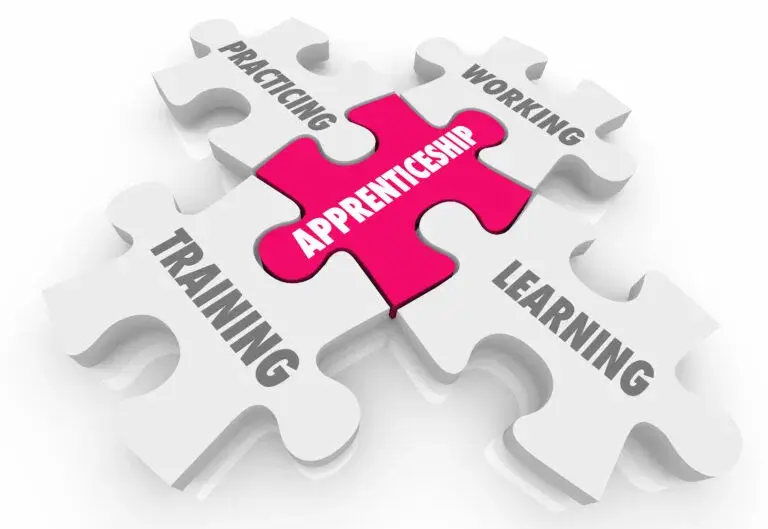
Apprenticeships - What Employers should consider
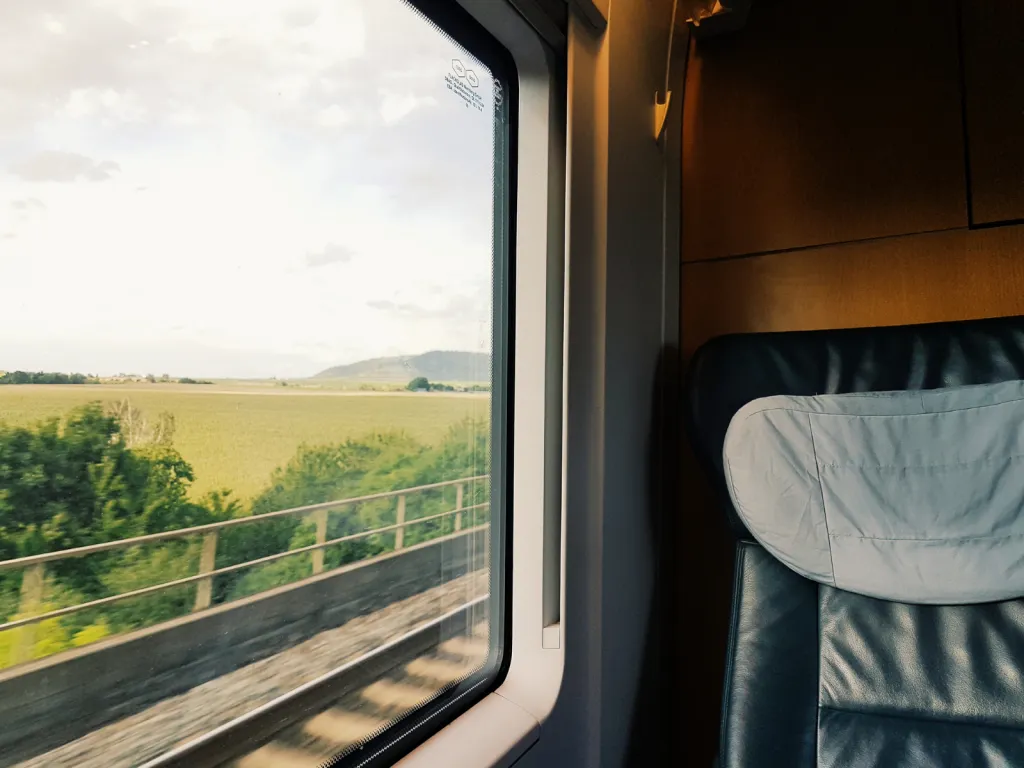
No Comments Yet
Let us know what you think