Deploying an improvement strategy – where you’re going wrong
The term ‘continuous improvement’ is a major industry buzzword in today’s climate of accelerating business change and the demand to not only survive but become a key player in the market.
It almost seems too simple, but is it really?
The main aim is about continually improving your whole business through processes and ways of working. However, it’s also how you approach planning, evolving, and implementing improvement strategies, which is where it can get complicated. There is an essential need to develop and nurture a philosophy of constant and sustainable improvement through empowering staff in the knowledge, tools and techniques required for this to be effective. This creates a mindset, makes staff accountable and reinforces the importance. Nevertheless, it must go beyond being a ‘fad’ and become the ‘normal daily way to operate’.
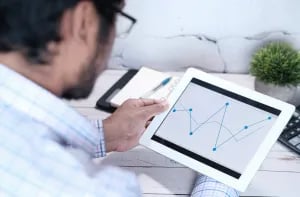
Continuous improvement is increasingly touted as a competitive differentiator, but all too often organisations are their own worst enemies. Just ask these simple questions:
- Does your organisational culture support change?
- Will there be fear of the change?
If your answers are no, then failure will happen because the key foundations of philosophy and culture are lacking. You quite simply cannot deploy an improvement strategy without these key foundations as they are factors that empower people. Remember, lean transformation must be considered as a strategy and not just a project. Firstly you must start by deploying a clear vision to the entire business including the direction being taken. In all honesty, this is rarely the case and without this the philosophy will fail through lack of understanding.
So where does it all go wrong?
From experience, businesses frequently underestimate the barriers to a successful implementation, causing perfectly good improvement strategies to fail.
So, what is causing so many deployments to falter?
One danger is that you might feel pressured to make changes simply to show that you are not sitting still. This is especially true if you do not actively pursue continuous improvement with your teams. An effective continuous improvement strategy requires a long-term, sustainable mindset and may not bear fruit in the extreme short term.
It takes high levels of self-discipline and be in it for the long haul.
The buy-in of key senior managers is essential to get an improvement strategy underway. However, if they are only focused on the end-goals rather than the work required along the way, disenchantment kicks-in, closely followed by total abandonment.
Experience shows that senior managers taking an active part in implementing an improvement strategy is incredibly important and will produce tremendous results in the morale of the team, which in turn produces excellent benefits as a strategy.
Without this, there will be no investment in the first place. And if there is no management commitment to adopt a new strategy, it will simply fail. Furthermore, if your improvement strategy is not aligned or does not support the wider business goals, why would senior managers spend their valuable time and resources on it? They wouldn’t!
It’s essential to ensure the improvements being implemented fit in with the overall wider strategy. This prevents it becoming substituted in favour of tasks that will further the key business objectives.
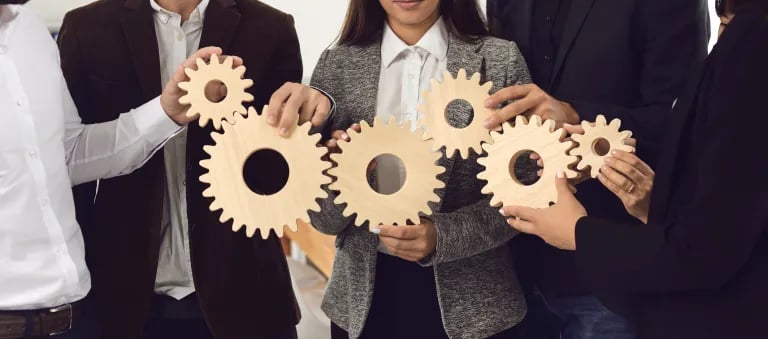
What else is there to consider?
Your decisions are only as good as the data that guides you.
Many a good improvement strategy fails due to inaccurate data. If followed, this data will only lead you down a different path and waste valuable resources. If you know that your data is unreliable, you can bet that the expected outcomes will be disappointing and unfavourable. Additionally, many improvement strategies stall as a result of not enough time and effort spent gathering data at the key measure stage. Without this important baseline, it’s easy to fall into ‘limbo’ as you can neither move forward nor prove any progress you have made.
Finally, many organisations deploy an improvement strategy without considering the key resources that are required e.g. time and people. Continuous improvement is mistakenly considered as something to be undertaken by a few select experts. This is not the case! All resources must be involved because there are just as many good improvement ideas in the brains of all staff doing their jobs, than just in the brains of a handful of experts.
Too often, business improvements are just bolted on as an extra task for staff to fit in alongside their already busy jobs. All this does is ensures that it becomes a low priority. If you truly want your improvement strategy to work, show belief and empower your staff to get actively involved – this will return the results you desire!
Give it your all
Undertaking a lean strategy takes time, dedication and an honest commitment. You cannot have a half-hearted approach or just do it when it suits. Believe in it and commit fully.
Fujio Cho (Toyota Honorary Chairman) quotes “Many good organisations try to practice Kaizen and use various TPS tools. But what is important is having all the elements together as a system. It must be practiced every day in a very consistent manner – not in spurts – in a concrete way on the shop floor.”
Share this
You May Also Like
These Related Stories
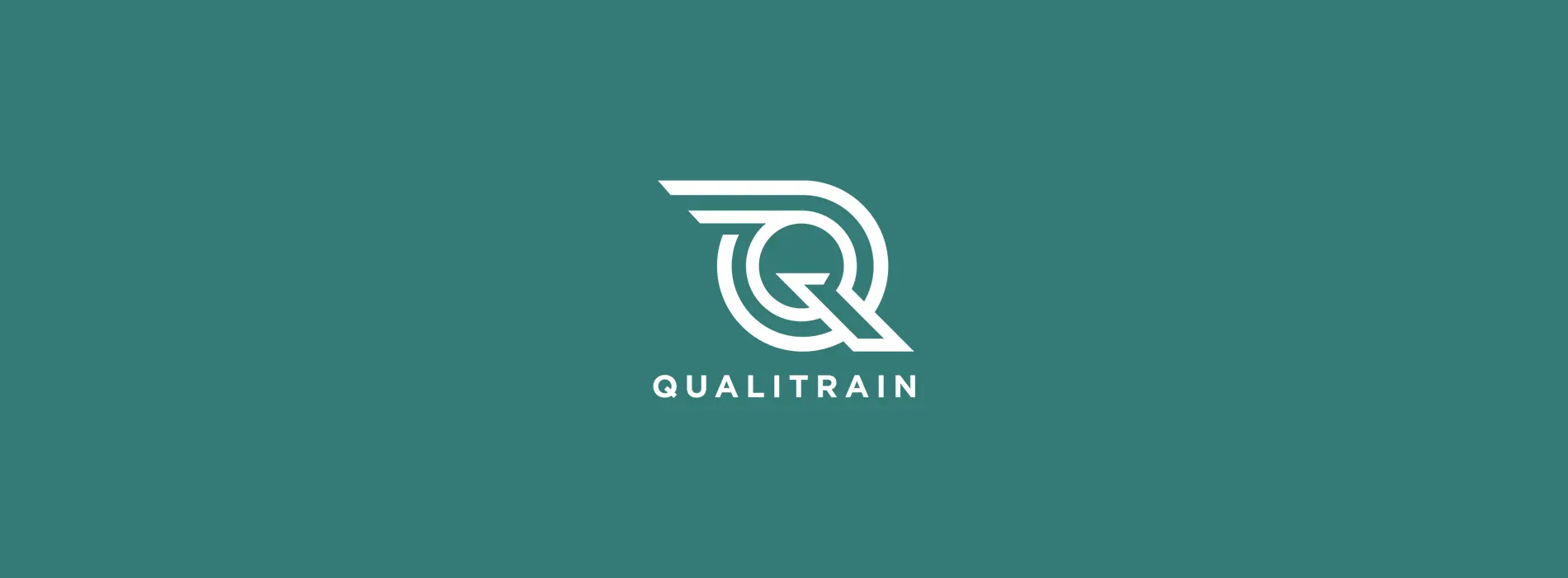
Understanding the Need for Continuous Improvement
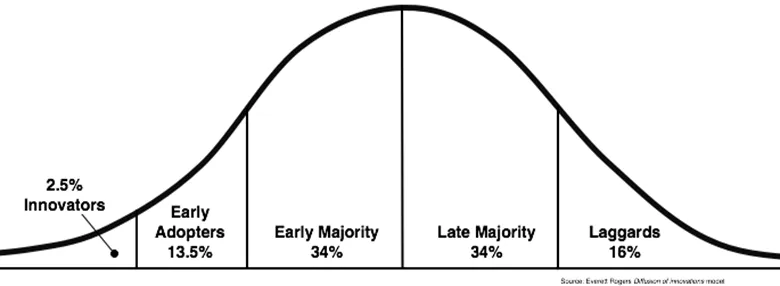
How to Influence Improvement in Your Team
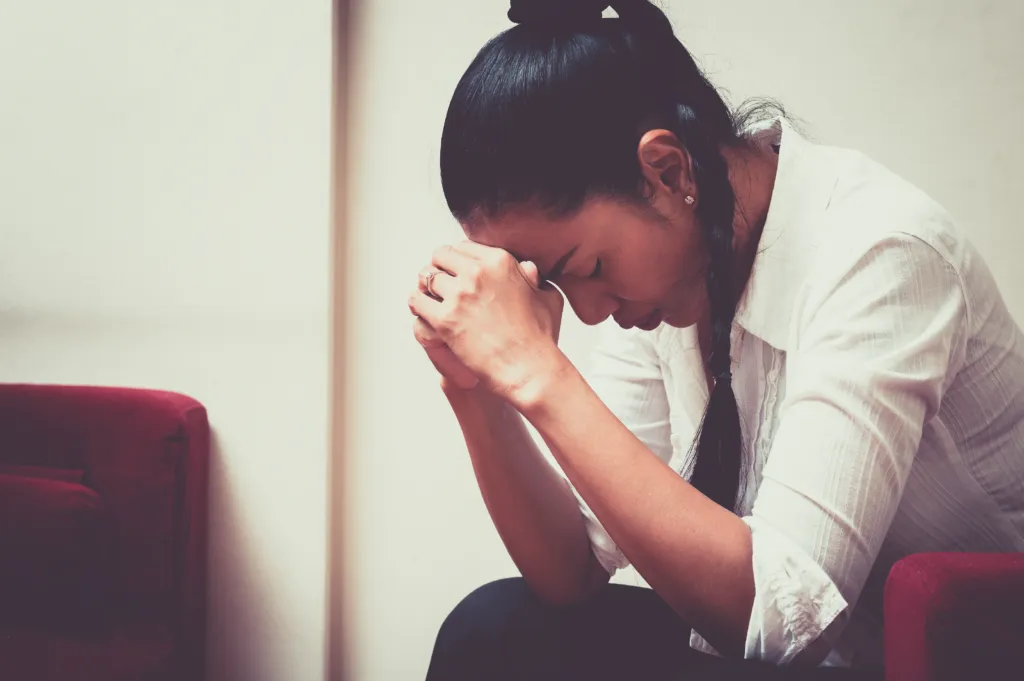
No Comments Yet
Let us know what you think